top of page
Generative Design Bike Frame
Background
This project started as part of a research project and continued as a senior design project. The International Olympic Committee wanted to showcase more technology and AI in sports. This led to the research group being formed, and the project commenced.
​
Unless otherwise mentioned, everything you will see below was directly done by me.
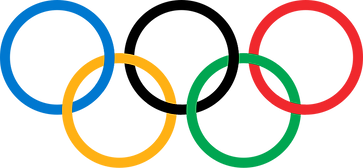
The Goal
Bridge the gap between organic generative designs and composite manufacturing.
​
Generative design produces very unique designs to achieve a goal that you give it. In our case, we want to minimize weight of the frame while still passing all regulations and standards (dictating by UCI and ISO guidelines). If you can make these organic, strange designs, you will see better performance. At least that's the theory.
Finite Element Analysis with Ansys
The bike frame was designed using Fusion 360's Generative Design Tool. However, Fusion 360 doesn't have a strong composites library and we had to make sure the design could withstand the load cases dictated by the International Organization for Standardization (ISO). Furthermore, Fusion does not have the capability to do fatigue analysis.
Ansys Composite PrepPost (ACP) allows us to do FEA on surface bodies based information on the carbon fiber - weave type, direction, number of plies, etc. I did FEA on all 5 loading cases, including 3 fatigue loading cases.
Below is an example of a load case for pedaling forces and the results under cyclic loading of 100,000 cycles
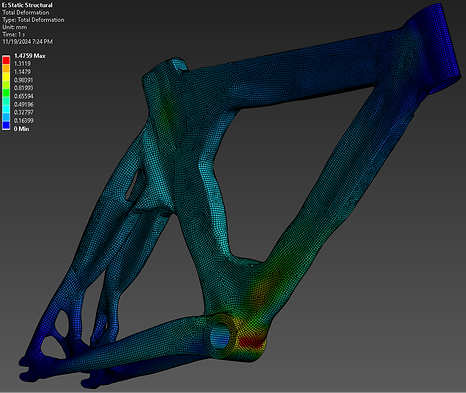

Max Deformation: 1.48mm
Minimum Factor of safety: 8.7
Negative Mold Design & Manufacturing
From the generative design, the following negative mold was made for the front half of the bicycle, which constitutes the majority of the surface area.
Both sides of the front half (left and right) are on the same stock piece of MDF stock in order to maintain consistency:
-
Even sanding on all sides
-
Mold sealant consistent
-
Even pressure across entire bike during vacuum bag​

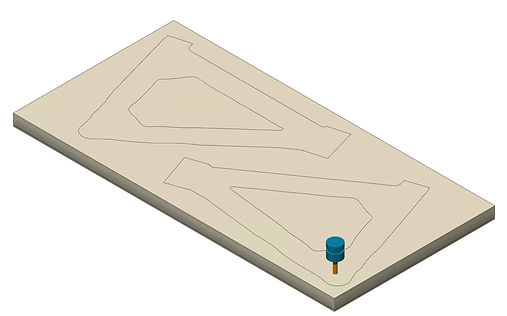
Summary of the CAM to manufacture the mold:
1. Adaptive clearing​​​ to get general shape (due to highly organic design)​​
​
2. Ramping operation along walls to get smooth finish on areas of high curvature (difficult to sand in corners)
​
3. Parallel operation to finish most organic areas
​
This was done with a Haas SR-100 CNC Gantry Router.
Live CAM (click to play)
Results & Post-Processing
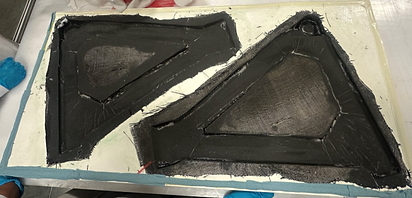
After Vacuum Bagging
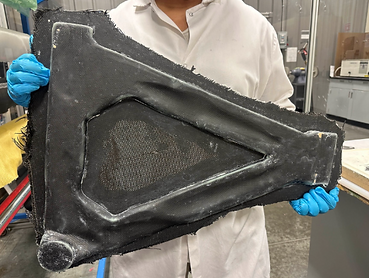
After Vacuum Bagging, removed from Mold

Post-Processed Front Half
Assembly & Final Steps
The back half of the frame was made using a 3-D printed PVA water-soluble mold. Once a layup was done around that, the PVA was melted out giving us the front and back half separately. 2 layers of carbon fiber were layed up around both halves together, acting as a bond to hold the entire bike frame together. Below is what the final bike frame looks

Final Bike Frame
bottom of page